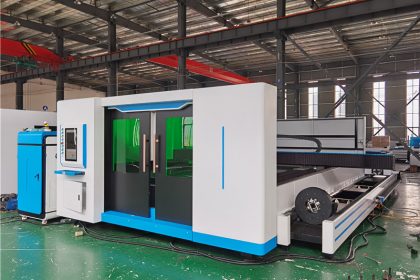
Why are there more and more ultra-high power metal fiber laser cutting machines on the market?
Ultra High Power metal fiber laser cutting machine
In view of these technical limitations, domestic laser equipment manufacturers have been actively seeking breakthroughs in the field of medium and heavy plate cutting. After continuous efforts and exploration, PRIMALASER finally achieved a milestone technical achievement: the newly launched S series v2.0 ultra-high power metal fiber laser cutting machine (Figure 1), the power can reach up to 30kW, with ultra-high speed , acceleration, supplemented by intelligent configuration and functions such as automatic edge finding, automatic nozzle replacement, automatic focusing, and non-sensing perforation, the overall performance and technical indicators have reached the international leading level, enabling fully automatic and unattended production.
main advantage
The equipment adopts pearlitic gray cast iron bed (Figure 2). Due to the existence of pearlite matrix, the strength and hardness of the parts are increased by 20% compared with those with ferrite matrix (Figure 3). There are small graphite flakes in the matrix. Compared with the welded bed and ordinary cast iron bed, the equipment can obtain higher structural rigidity, and can achieve excellent vibration damping effect and creep resistance.
Based on the above, under the condition of ultra-high speed and acceleration, the overall mechanical structure of the equipment still maintains the characteristics of small deformation and low vibration, so as to obtain extremely high machine tool accuracy, extend the customer’s equipment iteration cycle, and reduce the customer’s use cost.
Triangular ultra-high pressure honeycomb aluminum beam
Using aviation-grade aluminum alloy, the overall triangular ultra-stable structure has strong anti-torsion, anti-overturning performance and optimal mechanical properties; honeycomb-type inner cavity design, anti-deformation, can effectively disperse internal and external stress, high structural stability; High-pressure plastic production, compact structure, greatly improved strength, equipment-related characteristics are shown in Table 1.
On the one hand, the most stable structural form is obtained, and on the other hand, the rigidity of the gantry beam is improved. At the same time, the ultra-high pressure plastic production process is adopted to optimize and improve the principle, structure and production process to achieve the lightest weight and the highest rigidity. High-speed, high-precision application requirements.
Subversion function
⑴Intelligent processing.
The intelligent processing function can automatically identify and replace the nozzle according to the sheet thickness and material input by the user, and realize functions such as automatic calibration, edge finding, processing and platform exchange, which eliminates the repetitive operation of cutting sheets in batches and reduces labor intensity. Improve the user’s processing efficiency.
(2) Zero second senseless perforation.
1) Stepless perforation, which greatly reduces the perforation time by about 75% and improves the processing efficiency;
2) The continuous perforation stability is high, the waste hole rate is reduced from about 5% to 0.2%, and the integrity of the workpiece is improved;
3) High accuracy, less slag, stable follow-up, stable starting point, to ensure the best cutting section;
4) Reduce perforation time, save gas, reduce power consumption, reduce the risk of damage to lasers and cutting heads, and improve material utilization;
5) The packaging process can be learned and used immediately, and it can be simplified in one step for different processing scenarios and needs.
⑶ Thick plate limit small hole cutting.
In the field of laser cutting, the industry has always believed that the thickness of the plate is the minimum diameter of the cutting hole, and the S series achieves a minimum diameter of 0.2 times the thickness of the plate or even lower (Figure 4).
⑷ Perfect sharp corner cutting process.
The perfect sharp corner cutting process is a new process developed by Bond for high-quality carbon steel thick plate cutting. Compared with the previous standard cutting process, the new process has a faster bright surface cutting speed and a smaller section slope (35mm carbon steel single edge 15 wires) . Sharp corner cut products are shown in Figure 5.
⑸ The linkage speed is large. The fastest linkage speed: 200m/min; the maximum linkage acceleration: 4g. ⑹ Equipped with the world’s highest power equipment. S series v2.0 version is currently the world’s highest power laser cutting equipment, breaking the monopoly of foreign technology, the thickness of cutting stainless steel is increased to 130mm (Figure 6), carbon steel can reach 70mm (Figure 7), and it is also a medium and heavy plate. A subversive breakthrough in processing equipment.
concluding remarks
As an important type of plate in the industry, medium and heavy plate has been widely used in various fields, and its processing level is one of the important symbols of the development of related industries. The emergence of ultra-high-power metal fiber laser cutting machines in my country will make these industries usher in a quality Leap, PRIMALASER focuses on the development of the laser cutting field, and is committed to constantly breaking through new technologies and new processes, so as to truly meet the market demand and lead the development of the industry!